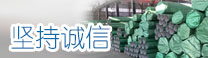
行業(yè)動(dòng)態(tài)
聯(lián)系方式
聯(lián)系人: 劉經(jīng)理
手 機(jī) :136 7673 1206
電 話 : 0577-28909778
E-mail : myzhide@126.com
厚壁不銹鋼管
您的位置:網(wǎng)站首頁(yè) > 新聞動(dòng)態(tài) > 厚壁不銹鋼管 > 正文不銹鋼管殘余應(yīng)力數(shù)值模擬的研究現(xiàn)狀
1998年,劉敏等人建立奧氏體不銹鋼圓管計(jì)算模型,分析多層對(duì)焊產(chǎn)生的殘余應(yīng)力。分析表明多層對(duì)焊后存在較大殘余應(yīng)力,在圓管內(nèi)側(cè)焊縫附近殘余應(yīng)力最大且為雙向拉應(yīng)力,并驗(yàn)證了該應(yīng)力將降低試件抗應(yīng)力腐蝕性能。
2000年,董俊慧等人利用ADINA非線性分析有限元程序,對(duì)低碳鋼管道環(huán)焊縫焊接殘余應(yīng)力進(jìn)行有限元分析。分析可得管內(nèi)焊縫及周?chē)鷧^(qū)域殘余拉應(yīng)力為主,隨著遠(yuǎn)離焊縫轉(zhuǎn)變?yōu)閴簯?yīng)力,管外殘余拉應(yīng)力為軸向應(yīng)力,管外殘余壓應(yīng)力為環(huán)向應(yīng)力。
2003年,徐勇等人應(yīng)用有限元分析軟件Marc建立了斜輥鋼管矯直機(jī)的壓扁矯正模型,模擬分析得到了矯直工藝會(huì)產(chǎn)生較大的殘余應(yīng)力,并得出溫矯直可有效降低殘余應(yīng)力。
2005年,董俊慧等人利用ANSYS有限元分析軟件,對(duì)耐熱鋼厚壁管環(huán)焊處殘余應(yīng)力進(jìn)行模擬分析,分析結(jié)果表明,焊縫處外表面殘余應(yīng)力小于內(nèi)表面殘余應(yīng)力,內(nèi)表面均為拉應(yīng)力,環(huán)向、軸向應(yīng)力大于徑向應(yīng)力,距外表層一定距離的位置出現(xiàn)殘余應(yīng)力最大值。
2006年,A.Yaghi等人分別對(duì)壁厚為7.1毫米和40.0毫米的不銹鋼管進(jìn)行4道和36道軸對(duì)稱對(duì)接焊縫的有限元分析。此外,還分析了內(nèi)徑與壁厚比為1到100的有限元模型,以研究管徑對(duì)殘余應(yīng)力的影響。研究表明,在薄壁焊管中,峰值拉伸應(yīng)力出現(xiàn)在靠近管子內(nèi)表面的地方,峰值壓縮應(yīng)力出現(xiàn)在靠近管子的外表面的地方,而在厚壁焊管中,峰值拉應(yīng)力出現(xiàn)在靠近管子外表面的位置,峰值壓縮應(yīng)力出現(xiàn)在靠近管子內(nèi)表面的位置。
2006年,Dean Deng等人基于ABAQUS有限元分析軟件,建立了3-D FE模型和2-D軸對(duì)稱FE模型,分析SUS304不銹鋼管多道焊縫中的溫度場(chǎng)和殘余應(yīng)力狀態(tài)。根據(jù)仿真分析可知,除了焊接開(kāi)始部分以外,圓周方向上的殘余應(yīng)力幾乎具有均勻的分布。內(nèi)表面和外表面上的軸向殘余應(yīng)力具有相反的分布。在焊接區(qū)及其附近,在內(nèi)表面上會(huì)產(chǎn)生拉伸軸向殘余應(yīng)力,而在外表面上會(huì)產(chǎn)生壓縮軸向應(yīng)力。遠(yuǎn)離焊接中心線,在外表面上形成軸向拉伸應(yīng)力,在內(nèi)表面上形成軸向壓縮應(yīng)力。在內(nèi)表面,環(huán)向應(yīng)力分布的形狀與軸向應(yīng)力非常相似。外表面上的環(huán)向應(yīng)力分布的形狀對(duì)距焊縫中心線的距離非常敏感。
2007年,武斌斌利用大型非線性有限云分析軟件MSC.Marc,對(duì)熱軋高強(qiáng)度無(wú)縫鋼管在熱處理過(guò)程中產(chǎn)生的殘余應(yīng)力進(jìn)行了研究?紤]熱力學(xué)相關(guān)影響因素,重點(diǎn)研究了鋼管淬火和回火的溫度場(chǎng)和應(yīng)力場(chǎng),并得到了與實(shí)際生產(chǎn)較為一致的結(jié)論。還分析了淬火溫度及冷卻率對(duì)鋼管殘余應(yīng)力的影響,得到920℃的最佳淬火溫度和減緩冷卻率有利于減少殘余應(yīng)力的結(jié)論。
2008年,李艷輝等人利用ANSYS/LS-DYNA有限元分析軟件,建立了無(wú)縫鋼管矯直的模型,并針對(duì)不同壓彎量進(jìn)行了對(duì)比,得出了結(jié)論,壓彎量越大,殘余應(yīng)力越大,環(huán)向和軸向殘余應(yīng)力在矯直之后均為外拉內(nèi)壓,且環(huán)向和軸向的應(yīng)力分布相對(duì)對(duì)稱且最大應(yīng)力出現(xiàn)在鋼管最后和棍子接觸的那部分區(qū)域。
2009年,李連進(jìn)等人利用MSC.Marc有限元分析軟件,以28CrMo47V無(wú)縫合金鋼管為研究對(duì)象,進(jìn)行了鋼管矯直過(guò)程的模擬分析。結(jié)果表明,殘余應(yīng)力與壓下量成正相關(guān),與溫度則成負(fù)相關(guān),同時(shí)也得出了鋼管的彈性模量與殘余應(yīng)力也呈正相關(guān)特性。
2010年,Kyong-Ho Chang等人利用三維(3-D)非耦合熱機(jī)械有限元(FE)分析方法對(duì)機(jī)械軸向拉伸載荷作用下不銹鋼管焊接殘余應(yīng)力進(jìn)行模擬分析。結(jié)果表明,沿圓周存在焊接殘余應(yīng)力的空間變化,并且在焊接開(kāi)始/停止位置存在殘余應(yīng)力的快速變化。當(dāng)在軸向?qū)雍附拥牟讳P鋼管上施加機(jī)械軸向張力時(shí),由于焊接引起的圓周收縮引起的焊接區(qū)域直徑的減小會(huì)在焊接區(qū)域產(chǎn)生二次彎矩,因此,會(huì)影響機(jī)械載荷下不銹鋼管焊縫中應(yīng)力的變化。
2011年,李革等人對(duì)鋼管相貫焊接殘余應(yīng)力進(jìn)行了模擬分析,分析得出,焊縫處等效應(yīng)力最大甚至超過(guò)屈服極限,環(huán)向殘余應(yīng)力接近屈服強(qiáng)度,引弧和落弧處殘余應(yīng)力有所波動(dòng),徑向殘余應(yīng)力在焊縫內(nèi)部出現(xiàn)峰值,等效殘余應(yīng)力隨著遠(yuǎn)離焊縫減少較快。
2012年,K.-H.Chang等人利用有限元焊接分析方法對(duì)600 MPa級(jí)高抗拉強(qiáng)度鋼管(STKT590)的管件殘余應(yīng)力分布進(jìn)行了模擬分析,并與STK490進(jìn)行對(duì)比研究。研究表明,除了焊接接頭附近的最大拉伸應(yīng)力外,兩個(gè)管道的環(huán)向殘余應(yīng)力均類(lèi)似分布。STKT590管道的內(nèi)表面應(yīng)力比STK490管道高136MPa。STKT590管的軸向殘余應(yīng)力幾乎等于STK490管的軸向殘余應(yīng)力。兩根管子的徑向殘余應(yīng)力均很小。除在焊縫附近觀察到的峰值應(yīng)力值外,兩根管子的有效應(yīng)力均顯示相似的分布。
2013年,A.H.Yaghi等人對(duì)P92鋼管中焊接金屬IN625的異種焊接引起的殘余應(yīng)力進(jìn)行了有限元模擬分析。分析發(fā)現(xiàn),在離焊縫和熱影響區(qū)不遠(yuǎn)的位置,焊管中有很高的拉應(yīng)力且建模變形塑性或規(guī)定高溫退火對(duì)殘余應(yīng)力有較大影響。
2013年,李陽(yáng)華等人利用ANSYS/LS-DYNA建立了V150油套管熱矯直的三維有限元模型,分析了矯直后環(huán)向和軸向殘余應(yīng)力的分布規(guī)律,得到了殘余應(yīng)力均成螺旋狀分布,并且環(huán)向殘余應(yīng)力具有外拉內(nèi)壓規(guī)律,而軸向外表面為拉應(yīng)力,內(nèi)表面則拉壓并存。
2014年,由于熱機(jī)械機(jī)制會(huì)產(chǎn)生殘余應(yīng)力,殘余應(yīng)力對(duì)裂紋萌生和擴(kuò)展具有重要影響,所以Jong Sung Kim等人用有限元模擬分析評(píng)估了感應(yīng)加熱彎曲鐵素體鋼管的殘余應(yīng)力。結(jié)果表明,鋼管外表面的殘余應(yīng)力高于其他區(qū)域且外表面的最大殘余應(yīng)力出現(xiàn)在彎曲端點(diǎn)附近。
2014年,Chin-Hyung Lee等人利用順序耦合的三維有限元分析方法對(duì)環(huán)焊奧氏體不銹鋼管和雙相不銹鋼管之間的殘余應(yīng)力進(jìn)行比較分析。分析結(jié)果表明,環(huán)縫焊接奧氏體不銹鋼管產(chǎn)生更高的軸向和環(huán)向殘余應(yīng)力,該殘余應(yīng)力在焊接起/停效果更顯著,并且它們應(yīng)力域更寬。與奧氏體不銹鋼管的環(huán)焊相比,環(huán)焊雙相不銹鋼管在焊接區(qū)域具有更高的峰值溫度和更高的冷卻速率。
2015年,N.Hempel·Th等人利用有限元模擬軟件對(duì)多道對(duì)接焊縫的鐵素體-珠光體鋼管中的殘余應(yīng)力進(jìn)行模擬分析。分析可得,沿管的軸向方向的應(yīng)力在管的外表面上明顯壓縮而在管的內(nèi)表面上拉伸,最大的軸向殘余應(yīng)力出現(xiàn)在內(nèi)表面的焊趾附近,且焊縫和熱影響區(qū)的相變都對(duì)殘余應(yīng)力有較大影響。
2016年,張莉等人利用ANSYS軟件對(duì)SA335-P92鋼管的焊接殘余應(yīng)力進(jìn)行了數(shù)值模擬分析。分析表明,該鋼管焊縫區(qū)周向殘余應(yīng)力為拉應(yīng)力,熱影響區(qū)出現(xiàn)了最大拉應(yīng)力。軸向殘余應(yīng)力為壓應(yīng)力,離焊縫越遠(yuǎn)殘余應(yīng)力越小。
2017年,李慧敏等人運(yùn)用SYSWELD軟件,以AISI304不銹鋼管為研究對(duì)象,針對(duì)環(huán)焊縫和縱焊縫兩種焊接殘余應(yīng)力進(jìn)行了相應(yīng)的數(shù)值模擬,驗(yàn)證了前人試驗(yàn)的正確性。并且分析得出,焊接速度和預(yù)熱溫度都會(huì)對(duì)兩種焊縫產(chǎn)生影響,適當(dāng)降低焊接速度并適當(dāng)提高預(yù)熱溫度將有利于降低殘余應(yīng)力。
2018年,姚茜以弦支穹頂結(jié)構(gòu)中的焊接空心球節(jié)點(diǎn)為研究對(duì)象,利用ANSYS有限元軟件進(jìn)行焊接空心球節(jié)點(diǎn)的焊接模擬,分析相應(yīng)的溫度場(chǎng)和應(yīng)力場(chǎng)。重點(diǎn)研究了管徑、球徑、壁厚等影響因素引起的殘余應(yīng)力變化規(guī)律和節(jié)點(diǎn)極限承載力和軸向剛度的變化規(guī)律。
2019年,彭景亮等人基于ABAQUS軟件平臺(tái),以SUS304不銹鋼管為研究對(duì)象,采用“熱彈塑性”法對(duì)鋼管焊接過(guò)程進(jìn)行模擬,并對(duì)該模擬過(guò)程的殘余應(yīng)力及變形情況進(jìn)行分析。分析表明,模擬所得的熔池形貌與試驗(yàn)一致,驗(yàn)證了模擬的合理性,同時(shí),鋼管軸向殘余應(yīng)力與角度無(wú)關(guān),而環(huán)向殘余應(yīng)力與角度有關(guān),試件由于殘余應(yīng)力發(fā)生了軸向和環(huán)向的收縮變形。
2020年,徐甄真等人對(duì)CT70連續(xù)油管高頻電阻焊接過(guò)程進(jìn)行模擬分析,探究焊接模擬后的殘余應(yīng)力值及其分布規(guī)律,同時(shí)調(diào)整焊接速度和擠壓量來(lái)研究其對(duì)殘余應(yīng)力的影響。得出結(jié)論為:焊縫處的不均勻加熱是導(dǎo)致其產(chǎn)生殘余應(yīng)力的主要原因,而遠(yuǎn)離焊縫處則是主要由擠壓產(chǎn)生殘余應(yīng)力。
文章作者:不銹鋼管|304不銹鋼無(wú)縫管|316L不銹鋼厚壁管|不銹鋼小管|大口徑不銹鋼管|小口徑厚壁鋼管-浙江至德鋼業(yè)有限公司
文章地址:http://wdtu.cn/Info/View.Asp?Id=1035
版權(quán)所有 © 轉(zhuǎn)載時(shí)必須以鏈接形式注明作者和原始出處
我們需要您的支持與分享
相關(guān)新聞
- 沒(méi)有資料