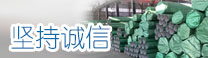
行業(yè)動態(tài)
聯系方式
聯系人: 劉經理
手 機 :136 7673 1206
電 話 : 0577-28909778
E-mail : myzhide@126.com
加氫裝置厚壁鋼管無損檢測方法的選擇
加氫裝置厚壁鋼管多,管道對接環(huán)焊縫無損檢測比例高,焊縫無損檢測工作量大,對接環(huán)焊縫無損檢測受現場條件制約,采用射線檢測往往存在一定難度,特別是隨著裝置大型化,該問題顯得更加突出。而射線檢測、超聲波檢測、磁粉檢測和滲透檢測作為常用的管道無損檢測方法,由于受其原理的限制,每種無損檢測方法均有其適用范圍和優(yōu)缺點,用單一的無損檢測方法難以保證焊縫缺陷檢出效果。在制定無損檢測方案時,應根據不同材質管道的特點和焊接過程中容易產生的缺陷類型,選擇兩種或多種檢測方法的無損檢測組合方案,從而保證無損檢測對缺陷的檢出效果,進而保證焊縫質量。
石油化工裝置管道的預制、安裝大多在現場進行,由于受現場施工條件限制和環(huán)境影響,安裝質量特別是焊接質量容易受到不良影響。因此選擇合適的無損檢測方法,能及時檢測發(fā)現焊接缺陷,進而消除焊縫質量隱患,是保證管道焊接質量的重要措施之一。
加氫裝置由于工況苛刻,厚壁鋼管多,高壓用厚壁鋼管焊縫無損檢測比例高,焊縫無損檢測工作量大。因此,厚壁鋼管焊縫的無損檢測往往是影響加氫裝置管道施工工期和質量的主要因素之一,隨著裝置的大型化,該問題更加突出。加氫裝置常用的厚壁鋼管材質如表1所示。管道公稱直徑一般為DN20至DN600,管道壁厚管表號范圍大多在SCH100至SCH160。
1常用無損檢測方法
無損檢測是指在不損害或不影響被檢測對象使用性能、內部組織的前提下,以物理或化學方法為手段,借助現代化的技術和設備器材,對試件內部及表面的結構、性質、狀態(tài)和缺陷的類型、性質、數量、形狀、位置、尺寸、分布及其變化進行檢查和測試的方法。
加氫裝置厚壁鋼管焊縫常用的無損檢測方法有:射線檢測(簡稱RT)、超聲波檢測(簡稱UT)、磁粉檢測(簡稱MT)和滲透檢測(簡稱PT),這些檢測方法統(tǒng)稱為四大常規(guī)檢測方法。其中RT和UT主要用于檢測試件內部缺陷,MT和PT主要用于檢測試件表面(近表面)缺陷。近年來,隨著衍射時差法超聲檢測(TOFD)、相控陣超聲檢測(PAUT)等新技術的不斷發(fā)展,使得焊縫檢測方法的選擇更加靈活。
2無損檢測的原理及特點
2.1射線檢測
2.1.1射線檢測原理
射線檢測的原理是基于射線通過密度不同的物質時,由于強度衰減不同,在底片上形成黑度差,使得缺陷影像在底片上得以顯現。射線檢測通常對體積狀缺陷(氣孔、夾渣)檢出率較高,這是由于氣孔、夾渣的密度與鋼的密度相差較大,在底片上容易形成黑度差而得以顯示。
當X射線和γ射線穿過被檢管道(管件)時,根據缺陷部位對射線的衰減,使底片上接收的射線劑量不同,使得膠片的黑度變化不同所形成黑白圖像,就可判斷出有無缺陷,以及缺陷的種類、數量、大小等。
2.1.2射線檢測的特點
射線檢測有以下主要特點:
(1)幾乎適用于所有管道材料,對檢測物體形狀及表面粗糙度無嚴格要求。
(2)可以獲得缺陷的投影圖像,檢測結果有直接記錄——底片。
(3)檢測成本高,對人體有傷害,必須考慮輻射防護問題。
(4)X射線照相檢測效率低且往往受現場作業(yè)空間限制,γ射線照相底片質量較低,且對安全防護要求高。
2.2超聲波檢測
2.2.1超聲波檢測原理
2.2.1.1脈沖反射超聲波
脈沖反射法是利用了超聲波在傳播過程中的反射原理,通過超聲波探傷儀探頭將電信號轉換為機械波發(fā)射脈沖超聲波,經過耦合介質在被檢工件中傳播,當遇到缺陷或其他不同物質的界面時即產生反射,返回的超聲波被探頭接收,并轉換為電信號在示波器上顯示脈沖回波,根據回波情況來判斷缺陷。
2.2.1.2衍射時差超聲波(TOFD)
衍射時差法超聲波檢測技術是在脈沖超聲檢測法的基礎上發(fā)展起來的一種新的檢測技術。其原理是利用缺陷端點的衍射波信號傳播時間差,進行發(fā)現缺陷和測定缺陷尺寸的一種超聲檢測方法,一般使用縱波斜探頭,采用一發(fā)一收模式。檢測結果以電子文檔保存,可打印輸出,它克服了脈沖反射超聲檢測無記錄的不足。
2.2.1.3相控陣超聲檢測(PAUT)
相控陣超聲檢測是一種通過對陣列傳感器的各獨立陣元按一定的延遲法則進行激勵、接收,合成特定形式的聲場,進行超聲波掃描成像檢測的技術。
通過改變壓電晶片陣列組合單元激勵電脈沖的延時值,可改變聲束聚焦深度、聲束角度和波型,由此可實現對工件中的各種方向性缺陷的有效檢測和對缺陷的準確定位和定量。相控陣檢測技術比起A超來說具有獨特的優(yōu)勢,如其扇掃掃查面積大、可達性好,同時進行B、C掃并有現場實時記錄功能,可以模擬缺陷的3D圖像等。同時也帶有A超的一些弊端,如缺陷的定性和缺陷自身高度的測量還有一定的難度等。
2.2.2超聲波檢測的特點
超聲波檢測有以下主要特點:
(1)應用范圍廣,適合檢驗厚度較大的工件,不適合檢驗較薄的工件。
(2)工件表面不平或粗糙會影響耦合和掃查。影響檢測精度和可靠性。
(3)檢測速度快,儀器體積小,重量輕,方便現場使用,衍射時差法缺陷檢出靈敏度高且有檢測記錄保存。
(4)無法得到缺陷的直觀圖像。定性存在一定困難。
(5)材質、晶粒度對探傷有影響,晶粒粗大的材料,例如鑄鋼、奧氏體不銹鋼焊縫,一般認為不宜用超聲波進行探傷。
(6)檢測結果受檢測人員影響大。
2.3磁粉檢測
2.3.1磁粉檢測原理
鐵磁性材料被磁化后內部產生很強磁感應強度,磁力線密度增大幾百倍到幾千倍。如果材料中存在不連續(xù)性(包括缺陷造成的不連續(xù)性和結構、形狀、材質等原因造成的不連續(xù)性),磁力線便會發(fā)生畸變,部分磁力線逸出材料表面,從空間穿過,形成漏磁場。漏磁場的局部磁極能夠吸引鐵磁物質,如磁粉,通過觀察磁粉痕跡達到檢測目的。
2.3.2磁粉檢測的特點
磁粉檢測有以下主要特點:
(1)缺陷顯示直觀,靈敏度高,可以發(fā)現極細小的裂紋以及其他缺陷。
(2)檢測速度快,操作簡單、成本低。
(3)適宜鐵磁材料探傷,不能用于非鐵磁材料檢驗。
(4)只能檢出表面和近表面缺陷,不能用于檢查內部缺陷。一般可檢出深度為1~2mm的近表面缺陷,采用強直流磁場可檢出深度達3~5mm的近表面缺陷。
(5)能用于檢測與磁場方向夾角較大的缺陷,不適用于檢測與磁場方向夾角小于20°或平行的缺陷。
2.4滲透檢測
2.4.1滲透檢測原理
零件表面被涂含有熒光染料或著色染料的滲透液后,在毛細管作用下,經過一定時間,滲透液滲進表面開口的缺陷中;在顯像劑的作用下回滲到工件表面;在一定的光源下(紫外線光或白光),缺陷處的滲透液痕跡被顯示(黃綠色熒光或鮮艷紅色),從而探測出缺陷的形貌及分布狀態(tài)。
2.4.2滲透檢測的特點
(1)滲透檢測可以用于除了表面疏松多孔性材料外任何種類的材料。
(2)效率高,可檢測形狀復雜的部件。
(3)不需要大型的設備,可不用水、電。
(4)只可以檢出表面開口缺陷,對埋藏缺陷或閉合型的表面缺陷無法檢出。
(5)檢測靈敏度比磁粉檢測低。
3管道安裝無損檢測方法的選用
3.1管道的無損檢測方法的選擇應考慮以下因素
(1)工件結構設計特點和材料特性;
(2)制造、焊接工藝和缺陷本身的特點;
(3)各種檢測方法的特點和檢測方案的適用性;
(4)可操作性及經濟性;
(5)檢測時機的正確選擇及抽查部位的代表性等等。
3.2管道焊接接頭的無損檢測
管道焊接接頭常見的外觀缺陷主要有咬邊、焊瘤、凹陷及焊接變形、未焊滿等,有時也出現表面氣孔和表面裂紋。單面焊的根部未焊透也位于焊縫表面。內部缺陷主要有氣孔、夾渣、裂紋、未焊透、未熔合等。焊縫的咬邊、焊瘤、凹陷及焊接變形、未焊滿等缺陷一般通過目視外觀檢驗即可發(fā)現。表面氣孔和表面裂紋一般借助磁粉檢測或滲透檢測來確定,而內部氣孔、夾渣、裂紋、未焊透、未熔合等埋藏缺陷只能通過射線檢測或超聲波檢測來發(fā)現。
射線檢測由于有底片作為記錄,對缺陷形狀反映直觀,容易被接受,所以,管道焊縫的檢測一般多采用射線檢測。但對于厚壁鋼管,如果采用射線檢測,由于曝光時間長、效率低。所以GB50517—2010《石油化工金屬管道施工質量驗收規(guī)范》規(guī)定“厚度大于30mm的焊縫可采用超聲檢測”。但由于超聲檢測受檢測人員影響因素大,缺陷記錄不直觀,缺陷定性困難,因此GB50517—2010又規(guī)定“設計文件規(guī)定射線檢測的焊接接頭改用超聲波檢測時應征得設計單位和建設單位同意”。
根據現場實際檢驗情況,對于厚度大于25mm的奧氏體不銹鋼管道,由于壁厚大,當采用雙壁單影透照時,X射線衰減嚴重而不能穿透。采用超聲波檢測,由于晶粒粗大,雜波較多,檢測靈敏度較低。而目前相關石油化工管道施工驗收規(guī)范對該問題并未給出可行的解決方案。
近年來,TOFD(即衍射波時差法)已正式頒布實施,開始應用于厚壁承壓設備的焊縫檢測,相對傳統(tǒng)的超聲波檢測,TOFD檢測對缺陷定量準確,對缺陷性質有一定判斷力,有檢測記錄。但TOFD仍未克服超聲波檢測的一些缺點:比如對檢測圖像的識別、缺陷性質的判斷準確性受人為影響較大,檢測設備投資較大等。而對于管道而言,由于管道口徑相對較小,曲率大,壁薄,所以僅在大口徑厚壁鋼管上逐步使用。另外相控陣超聲檢測技術,近期也逐漸應用于管道無損檢測。
4無損檢測的難點及解決辦法
根據目前施工規(guī)范的要求,加氫裝置厚壁鋼管對接焊縫一般采用RT檢測,對碳鋼和合金鋼管道角焊縫采用MT,對奧氏體材料管道角焊縫采用PT檢測。但對于現場安裝的對接環(huán)焊縫,當采用RT檢測時,多采用雙壁單影透照,當管道壁厚大于25mm時,由于受X射線機的能力限制,只能γ射線檢測。但是由于γ射線檢測對安全防護距離要求較遠,在裝置現場往往難以達到要求,特別是對于周邊有其他運行裝置或施工的情況下,更是無法滿足安全防護要求。由于射線檢測需要防護的原因,檢測期間現場無法開展其他作業(yè),在工期控制上也帶來嚴峻的考驗。因此,無損檢測往往成為加氫裝置厚壁鋼管施工的難點。
根據項目的具體實施情況,對于加氫裝置厚壁鋼管的環(huán)焊縫,目前常用的檢測方法有如下幾種方案:
(1)對碳鋼、合金鋼管道對接環(huán)焊縫焊接厚度達到大約25mm時,停止焊接,進行RT檢測,RT檢測合格后,繼續(xù)完成焊接,然后進行UT檢測+TOFD檢測+MT檢測。
(2)對碳鋼、合金鋼管道對接環(huán)焊縫焊接厚度達到大約25mm時,停止焊接,進行RT檢測,RT檢測合格后,繼續(xù)完成焊接,然后進行UT檢測+MT檢測。
(3)對奧氏體不銹鋼管道對接環(huán)焊縫焊接厚度達到大約25mm時,停止焊接,進行RT檢測,RT檢測合格后,繼續(xù)完成焊接,然后進行UT檢測+PT檢測。
(4)對奧氏體不銹鋼管道對接環(huán)焊縫焊接厚度達到大約25mm時,停止焊接,進行RT檢測,RT檢測合格后,繼續(xù)焊接,逐層進行PT檢測,然后進行UT檢測。
(5)對碳鋼、合金鋼管道對接環(huán)焊縫焊接完成后進行UT檢測+TOFD檢測+MT檢測,并抽取一定比例進行RT檢測。
(6)對奧氏體不銹鋼管道對接環(huán)焊縫焊接完成后進行UT檢測+PT檢測,并抽取一定比例進行RT檢測。
上述每種檢測方案都有其特點,由于UT檢測對裂紋等面積型缺陷較敏感,對于碳鋼、合金鋼管道而言,宜選用上述方案(5)。特別是對于合金鋼管道,當選用方案(1)或方案(2)時,如果中間停止焊接還需要進行后熱處理,否則容易產生裂紋缺陷。而對于奧氏體不銹鋼管道,由于焊縫晶粒粗大,晶界反射雜波強,對其厚壁鋼管UT檢測效果并不理想,因此宜選用方案(4)或方案(3)。
當然,要保證焊接質量,最根本的措施還是從焊接工藝、焊接材料、焊接過程控制、焊后熱處理、焊接設備、焊接人員等方面進行綜合控制,然后選用適當的無損檢測方案,從而獲得良好的焊接接頭質量。根據目前的施工情況,建議加大管道的預制深度,減少現場的安裝工作量,為焊接及無損檢測提供良好的施工環(huán)境。
另外,隨著無損檢測設備和技術的進步以及檢測工藝的成熟,應及時修訂相關的管道施工驗收規(guī)范,使無損檢測新技術能及時應用于管道檢測,并符合標準規(guī)范的要求。
5結論
由于每種無損檢測方法都有其優(yōu)點和局限性,因此在選用無損檢測方法時,應根據材料特性、結構特點,可能出現的缺陷類型等因素綜合考慮,選用合適的無損檢測方法,有時還需要采用2種或多種無損檢測方法對管道進行綜合檢測,以準確判斷缺陷。另外,通過加大管道的預制深度,減少現場的安裝工作量,為管道焊接及無損檢測提供良好的施工環(huán)境,是提高管道施工質量的措施之一。
文章作者:不銹鋼管|304不銹鋼無縫管|316L不銹鋼厚壁管|不銹鋼小管|大口徑不銹鋼管|小口徑厚壁鋼管-浙江至德鋼業(yè)有限公司
文章地址:http://wdtu.cn/Info/View.Asp?Id=1131
版權所有 © 轉載時必須以鏈接形式注明作者和原始出處
我們需要您的支持與分享
相關新聞
- 沒有資料