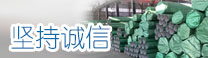
行業(yè)動態(tài)
聯(lián)系方式
聯(lián)系人: 劉經(jīng)理
手 機 :136 7673 1206
電 話 : 0577-28909778
E-mail : myzhide@126.com
厚壁不銹鋼管
您的位置:網(wǎng)站首頁 > 新聞動態(tài) > 厚壁不銹鋼管 > 正文昆鋼2500m3高爐熱風管道溫度異常分析及處理
本文對昆鋼2500m3高爐熱風管道發(fā)生溫度異常狀況的處理實踐進行了總結和分析。針對昆鋼2500m3高爐在開爐6年多后出現(xiàn)的熱風管道部分區(qū)域溫度升高的情況進行原因分析,并根據(jù)情況對溫度異常部位進行澆注處理,取得了較好的效果,有效抑制了溫度的進一步升高,避免了熱風管道燒穿惡性事故的發(fā)生,為高爐穩(wěn)定生產(chǎn)奠定了基礎。
1前言
昆鋼新區(qū)2500m3高爐(以下簡稱1#高爐)于2012年6月26日開爐投產(chǎn),有效容積2500m3,配備3座改進型頂燃式熱風爐,使用風溫1200℃。自開爐達產(chǎn)以來取得了較好的生產(chǎn)經(jīng)濟指標,高爐產(chǎn)量7000t/d,燃料比520kg/t,在全國同類型高爐處于領先。1#高爐開爐6年多來,一直使用高風溫進行操作。自2016年1月下旬開始,昆鋼新區(qū)1#高爐熱風爐管道部分區(qū)域溫度明顯升高。通過紅外線測溫儀及熱成像測量發(fā)現(xiàn),共有熱風主管與圍管三岔口、混風室進風與熱風主管三岔口、混風室出口與熱風主管三岔口、1#熱風爐支管與主管三岔口、1#風爐出口、1#熱風爐支管、2#熱風爐支管與主管三岔口、2#熱風爐出口、2#熱風爐膨脹節(jié)、3#熱爐出口、3#熱風爐支管與主管三岔口等11個區(qū)域溫度區(qū)域出現(xiàn)溫度異常。針對這一情況,昆鋼新區(qū)煉鐵廠利用計劃檢修機會,分別對熱風管道溫升幅度較大的區(qū)域進行灌漿和澆注處理。從處理后的結果看,取得了一定的效果,有些區(qū)域溫度明顯降低,但有些區(qū)域因停爐時間短處理不徹底效果不明顯,溫度持續(xù)偏高,繼續(xù)惡化將進一步影響高爐生產(chǎn)。為了消除生產(chǎn)隱患,2018年5月,新區(qū)煉鐵廠利用高爐降料面噴涂造襯長期停爐時機對熱風管道高溫區(qū)域進行澆注處理。處理后效果明顯,溫度得到控制,通過開爐后一段時間的跟蹤測量,溫度都處于規(guī)定范圍內,為高爐穩(wěn)定生產(chǎn)奠定基礎。
2熱風管道溫度異常原因分析
2.1結構特點
熱風爐熱風管道體系結構很復雜,有垂直管道、彎管、拉桿、膨脹節(jié)、支座等構成,而且還是一組高溫、高壓管道。正常生產(chǎn)情況下,熱風管道承受的熱風溫度為1100~1300℃,壓力為0.3~0.6MPa;管道工作層耐火磚的平均溫度可達1000~1300℃,管殼正常溫度為80~150℃。管道在工作時的高溫、高壓作用下極易產(chǎn)生線性膨脹,其對管道系統(tǒng)的破壞作用表現(xiàn)為:在管道垂直處、封頭、彎頭處、不對稱開孔處等凡有阻擋氣流趨勢的地方都會產(chǎn)生盲板力,在巨大盲板力作用下管道會產(chǎn)生位移、變形,造成管殼交界處出現(xiàn)較大的變形量。外部鋼殼的變形必將擠壓內部磚襯,磚襯極易被擠碎,造成串風引起管殼溫度的升高,進而出現(xiàn)變形加劇,最終出現(xiàn)管殼發(fā)紅、開裂、內襯變形掉磚等問題。
2.2熱風管系磚襯設計
熱風管系結構復雜,其承受的高溫熱應力和高壓力致使管道產(chǎn)生膨脹。雖然設置了波紋補償器和拉桿來消除管道的膨脹力,但是由于工況不同產(chǎn)生的工況應力變化不盡相同,導致各波紋補償器工作的無序和混亂。熱風總管與支管垂直相連,熱風總管的熱膨脹無序和混亂必將造成個別熱風支管橫向變形過大,耐火磚內襯將受擠壓而損壞。所以在熱風管系磚襯的設計中不但要提高磚襯的整體穩(wěn)定性,在熱風出口和三岔口還應采用組合磚砌筑,同時加厚工作層磚襯和將管道上半圈部分隔熱耐火磚改為重質澆注料來增強抗應力性。而昆鋼新區(qū)1#高爐熱風爐的隔熱磚選擇為輕質粘土隔熱磚易被管道變形擠壓損壞,導致竄風引起管殼溫度升高、發(fā)紅,圖1。
2.3砌筑質量問題
熱風管道施工質量的好壞將直接影響熱風爐的壽命,磚縫的均勻性、灰漿的飽滿程度都影響熱風爐砌體結構的穩(wěn)定性。磚縫偏大、灰漿不飽滿在外力作用下灰漿容易被擠碎形成空縫,引起串風導致爐殼溫度升高、發(fā)紅。更甚者在形成空縫后側邊的磚在外力作用下易被擠動,最終松動脫落。昆鋼新區(qū)1#高爐熱風爐的熱風管道在砌筑施工過程中也存在類似問題,特別是在三岔口管道垂直交接地方易出現(xiàn)問題(圖2)。
2.4烘爐存在不均勻情況
熱風爐烘爐時,燃燒產(chǎn)生的熱煙氣幾乎被煙道抽走,只有極少一部分煙氣能烘烤到熱風出口,熱風支管、主管、圍管烘爐時烘烤不到,只有烘高爐時才能烘烤到。烘高爐時烘烤時間周期短、溫度低,造成熱風管道烘烤達不到要求,泥漿烘烤溫度不夠,泥漿粘接強度不夠,高爐投產(chǎn)送風時,磚縫泥漿易被吹走形成空縫,導致熱風管道砌體串風、管殼溫度高發(fā)紅,甚者垮磚影響風溫、影響高爐生產(chǎn)。
3熱風管道澆注
3.1澆注前的準備工作
為了消除生產(chǎn)安全隱患,新區(qū)煉鐵廠決定利用2018年5月降料面停爐噴涂造襯的機會對熱風管道溫度高的區(qū)域進行挖補澆注處理。通過停爐之前對熱風管道的跟蹤監(jiān)測及溫度測量,發(fā)現(xiàn)3座熱風爐熱風出口、三岔口、混風室出口區(qū)域溫度較高,各區(qū)域溫度情況見表1。
從表中可看出各區(qū)域溫度都在200℃左右而且還有進一步升高的趨勢,如果不處理最終將可能因熱風管道出問題影響生產(chǎn)。
3.2澆注
由于此次停爐時間較長,有充足的時間來處理管道存在的問題,停下來后先冷卻一段時間然后對各區(qū)域開孔,開孔后冷卻到溫度合適時再進行支模、澆注、焊接等工序工作。
3.2.1開孔情況
根據(jù)測溫跟蹤情況分別對3座熱風爐熱風出口、三岔口、混風室出口開孔。開孔時在需要澆注的區(qū)域割除鋼殼、清除磚襯,待冷卻后進行支模澆注,開孔情況如下圖3所示。
3.2.2澆注料的選擇
根據(jù)情況,此次澆注后不再單獨進行烘干,而是利用管道自身的溫度烘干。根據(jù)熱風管道的工作工況,澆注料選擇牌號為YQ-50的耐高溫、耐沖刷的高鋁高強快干隔熱壓入料,其理化性能指標見表2。
待溫度降到合適后,先把需要澆注開孔區(qū)域周邊松動磚取走,并盡量修規(guī)整,清理干凈管道內部的磚。其次內弧支模,為了方便,此次澆注所用模具就在現(xiàn)場臨時用圓弧鋼板代替,模支好并固定牢固,用纖維粘堵嚴鋼板與磚襯之間的縫隙。支模工作完成后進行澆注,澆注料要低于管壁,澆注完成后將割好的鋼殼焊接好,然后在鋼殼上開孔灌漿,最后通過自然烘烤干后再進行一次灌漿。灌漿完后到管道內拆除模具及支架,至此澆注結束。支模情況如圖4所示。
4效果檢查
高爐復產(chǎn)后對所有澆注區(qū)域進行效果檢查,通過跟蹤測量溫度并做好記錄,具體情況如表3所示。
從表中可看出各區(qū)域的溫度與澆注前(表1中溫度)都有明顯下降,降幅達50~80℃,而且后期測量的溫度也比較穩(wěn)定,都保持在一個合理的水平,證明澆注層工作良好,起到了預期效果。
5建議
通過昆鋼新區(qū)1#高爐熱風爐管道溫度異常分析及處理,結合學習、了解到的最新熱風爐技術得出以下幾點建議:
(1)鑒于熱風管系結構復雜性及工作環(huán)境,在熱風爐設計時就要考慮降低盲板力、減小管徑膨脹應力,從而減小因管道變形對磚襯產(chǎn)生的擠壓而損壞磚襯。
(2)隨著煉鐵技術的發(fā)展,紅外線熱成像儀已經(jīng)很好的運用于高爐煉鐵,并取得好評,建議在熱風爐管道管殼加裝智能紅外線熱成像儀,時時監(jiān)控管殼溫度,避免因管道溫度異常,磚襯垮塌影響生產(chǎn)。
(3)由于管徑變形對磚襯產(chǎn)生擠壓損壞磚襯,引起掉磚甚至垮塌,建議三岔口上半環(huán)采用耐高溫、耐擠壓、高強度的耐火材料直接澆注。
(4)基于熱風爐烘爐時熱風管道烘烤存在的問題,在熱風爐烘爐時建議通過倒流休風閥、熱風管道人孔安裝臨時煙氣引風機引煙氣對管道進行烘烤,達到烘烤目的和要求。
6結語
(1)熱風管道破損的原因較為復雜,熱風管道的長壽是一項系統(tǒng)工程。為保證熱風管道長壽,須從設計、耐材選擇、砌筑施工、烘爐就要嚴格把關,精心做好每一道工序;另外在使用過程中要做好平時的維護,定期測溫做好記錄,發(fā)現(xiàn)異常要及時處理。
(2)熱風爐烘爐及投產(chǎn)后的高溫工作環(huán)境,使熱風爐砌體水分蒸發(fā)后產(chǎn)生間隙。所以根據(jù)經(jīng)驗,在投產(chǎn)一段時間(一般3~5個月)都要對熱風爐進行整體灌漿封堵間隙,如熱風管道砌體與鋼殼之間、耐材之間的間隙,避免竄風引起管道溫度升高,甚至發(fā)紅,出現(xiàn)異常情況。
(3)澆注處理過程雖然不是很復雜,但開孔位置的確認、支模、澆注料的選擇、澆注完后的灌漿等都要嚴格按操作規(guī)程進行。
(4)此次澆注處理熱風管道取得了良好效果,也為今后處理類似問題積累了經(jīng)驗。
文章作者:不銹鋼管|304不銹鋼無縫管|316L不銹鋼厚壁管|不銹鋼小管|大口徑不銹鋼管|小口徑厚壁鋼管-浙江至德鋼業(yè)有限公司
文章地址:http://wdtu.cn/Info/View.Asp?Id=1115
版權所有 © 轉載時必須以鏈接形式注明作者和原始出處
我們需要您的支持與分享
相關新聞
- 沒有資料